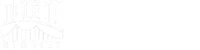
Legacy of Glass
Special | 50m 17sVideo has Closed Captions
Legacy of Glass chronicles the art glass movement and how it began in Toledo.
Legacy of Glass chronicles the art glass movement and how it began in Toledo with the help of 2 men, Harvey Littleton, a ceramics instructor at the Toledo Museum of Art, enlisted the aid of engineer Dominick "Nick" Labino to create a formula for glass that could be melted in small batches in furnaces for the purpose of creating pieces of art.
Problems with Closed Captions? Closed Captioning Feedback
Problems with Closed Captions? Closed Captioning Feedback
Toledo Stories is a local public television program presented by WGTE
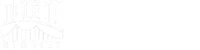
Legacy of Glass
Special | 50m 17sVideo has Closed Captions
Legacy of Glass chronicles the art glass movement and how it began in Toledo with the help of 2 men, Harvey Littleton, a ceramics instructor at the Toledo Museum of Art, enlisted the aid of engineer Dominick "Nick" Labino to create a formula for glass that could be melted in small batches in furnaces for the purpose of creating pieces of art.
Problems with Closed Captions? Closed Captioning Feedback
How to Watch Toledo Stories
Toledo Stories is available to stream on pbs.org and the free PBS App, available on iPhone, Apple TV, Android TV, Android smartphones, Amazon Fire TV, Amazon Fire Tablet, Roku, Samsung Smart TV, and Vizio.
Narrator: Toledo, Ohio.
For most of the 20th century, it was known as the Glass City home to factory furnaces that produced tableware, automotive and industrial glass for generations.
But the invention of Michael J. Owens bottle making machine revolutionized the glass industry, and the factories transitioned from the painstaking, handmade work of old world craftsman to the rapid fire reproductions of machines marking the end of the industrial glass blowers.
But the vision of Harvey Littleton and a workshop at the Toledo Museum of Art in 1962 would take glass out of the factories and open a new world for glass blowers as artists creating and endlessly evolving legacy of glass From its inception, glassblowing has been a commercial pursuit.
Its products were beautiful to look at, but reflected mass production and marketing strategies over subtlety of form and esthetic values.
Until Harvey Littleton an artist with a distinguished glass pedigree, began to question the status quo.
Jack Schmidt: Harvey came from a very technical background.
His dad was Jesse Littleton, who developed Pyrex, and he was kind of the black sheep artist in the family Harvey wanted to show everybody that you didn't have to be affiliated with a major industry or factory to make art out of glass, that you could build a little box and put it in your garage and run a gas pipe into it.
And melt glass and make stuff and that it really should be introduced as a material for artists to use for self-expression.
Tom McGlauchlin: Artists that wanted to work with glass had to be designers, and they would draw pictures of what they wanted made.
And though the workmen in the factory would make the objects.
And his father told him that's what he should do.
If he wanted to work in glass, he should be a designer for Stu Ben.
But he knew that the designers to Ben would spend months working on a design, and then the salesmen, the stubborn salesman, would decide that it wouldn't sell, and it wouldn't get produced.
And he thought that frustration was intolerable.
So he wanted to be an artist and design the work and make it himself.
Narrator: While nurturing his dream of blowing glass, Harvey Littleton took a job teaching ceramics at the Toledo Museum of Art.
Otto Wittman was the museum's young and dynamic assistant director, and they developed a good working relationship.
Although Littleton eventually went on to teach at the University of Wisconsin, he never forgot his days in Toledo.
And after years of trying and failing to secure funding for a glassblowing class he turned to his old friend, Otto Wittman, now director of the Toledo Museum of Art.
For help during the fifties.
Havery Littleton: I went back to Otto for recommendations for things like the Guggenheim or some other grant that I was applying for And finally, that's what happened, how it got started with the workshop.
He said, Well, it looks like if anything's going to happen on this glass thing, we'll have to do something here.
Otto Wittmann: He had a theory that one ought to be able to make glass the same way you make pottery I said, Well, how are you going to do that?
He said, Well, I've got to invite a few of my friends in the pottery business who are teaching pottery, and we're going to come together in the summer.
And we're going to try to melt some glass and make some see if we can't do it.
And how about doing it?
TOLEDO Narrator: Otto Whitman arranged for the workshop to take place in a garage on the museum grounds.
He also contacted Dominic Ladino, an old friend who happened to know a little something about Glass.
Tom McGlauchlin: He was an amateur potter.
He was an amateur, an analyst.
He made paper.
He had done some painting He tried everything.
And I think art or simply thought this was something that Nick should do simply because Nick was interested in every kind of artistic pursuit.
But Nick was particularly interested in glass.
He was vice president and director of research for Johns Manville.
Fiberglass in Toledo, and he had a knack for problem solving.
He held dozens of patents for technical advances in the science of Glassmaking, including insulating technology used in the Apollo moon missions and the heat resistant tiles for the space shuttle.
Libby now would provide the technology for Lyttleton stream.
Norman Schulman: Harvey.
I met an auto witness office.
He was energetic very positive.
He had complete faith in himself and what he was doing.
Narrator: Norm Shulman was the ceramics instructor at the Toledo Museum of Art and became the liaison between Otto Whitman and the glass blowers.
Norman Schulman: I felt it was a good thing.
I think I felt educationally it was good.
I, I, I knew the class was just a beautiful material and that if something came of it, it would be well worthwhile.
And if nothing came of it, well, you know, as the old saying, nothing ventured, nothing gained.
Harvey Littleton: We cooked up a letter which we wrote to the deans of University of Michigan, University of Indiana, and a number of other schools inviting my friends to take part in this historic workshop, which we had no idea anything would happen.
But we we did it anyway.
And so their schools sent them to to Toledo.
Edith Franklin: Harvey at that time was teaching at the University of Wisconsin.
He was teaching ceramics.
Clayton Bailey was one of his assistants, and the others were potters and heads of their ceramic departments.
At the universities that they came from.
And Tom Mcglothlin was the ceramic teacher in Iowa.
Tom McGlauchlin: I was so worried that I was limited to ten people and I was so worried that I wasn't going to get in, that I called the museum right down and signed up for it and that I didn't have to.
I found out I didn't have to worry because they only got nine people on I got the 10th here in Toledo from one of Harvey Farmer students.
Edith Franklin: I was in the right place at the right time.
I was in Norm Shulman's class when he announced this new experiment that was going to start that they were going to have a glass workshop, and it was only for university teachers.
Therefore, I was not eligible But then about a week before it started, Norm Shulman said, If you still would like to take the class, you can.
It didn't fill, so you can take it.
It's $50 and I paid my $50 fast and I took it.
Tom McGlauchlin: It took place during spring vacation and I rode out to Toledo with Harvey and Clayton Bailey, and we got here.
We went to Norm Sherman's house and spent the night in his basement on cots.
And we were awake all night all three of us.
I never said a word to each other.
I assume the others were asleep.
I guess because we were all so excited about what was going to happen.
The next day that we couldn't sleep.
Narrator:The initial excitement everyone felt soon turned to frustration when things didn't go as well as expected.
Tom McGlauchlin: We got a furnace built and put a fur burner in it and got it hot.
And Harvey's plan was to put stoneware pots that he had actually thrown himself into the kill and put chemicals in the pots, use the pots, as crucibles, to hold the chemicals, to melt them into glass.
Harvey Littleton: So we mixed the glass and melted it.
Well, it didn't melt very good because we had screwed up the formula.
So then we called on Nick.
Nick came in and looked at it and said, you got to get rid of all that stuff.
And so we did by tearing the furnace apart Tuesday night.
We took it apart and we had it back together again by Wednesday.
And Nick brought us some of his marbles that they use to make fiberglass.
And we just threw them in and melted them.
And then by Wednesday night, we had we had glass to play with.
We immediately split up into groups so we could blow glass all night.
Tom McGlauchlin: I think everybody kind of looked at it and put rods into a pond and blow pipes into it and kind of just see what the consistent was like and what it was like.
But we didn't know what we were doing.
I think we'd seen a movie and the Museum of Glass Floors.
My lack of skill was unimportant.
It was just very exciting just to work with it.
Harvey Littleton's dream was taking shape, and the future of hot glass quickly attracted the interest of its past masters.
Norm Schulman: My feelings were that since we were in Toledo, we should involve the old glass blowers.
I just felt that they would have information that would be useful to us.
I felt that if we had some sort of a public program and send invitations that somebody would show up.
Tom McGlauchlin: He'd gotten some publicity on The Blade about the workshop, and he said that he was going to have a lecture on Saturday morning in the museum theater to talk about glass as a medium for artists and what they'd accomplished.
Norman Schulman: And Harvey gave a lecture, and after the lecture he had these pieces of glass out there and talking.
And this old guy came over and me holding it and everything, and he started talking to Harvey, and it turned out that indeed he was sort of the dean of the old glass blowers as Harvey Leaf Crane.
Tom McGlauchlin: Harvey Leaf Crane was very impressed.
He said this is You've never blown glass before and you're making these things.
And so he had immediately see our furnace.
So we all trooped out to the garage behind the museum where the furnace was.
And he immediately he came in a in a black suit and a white shirt and tie to this lecture.
And he immediately started blowing glass for us and demonstrated.
And then each of us asked each of us what we wanted to make, what kind of object we'd like to make in glass.
And then he showed us exactly how to do it.
Harvey Littleton: And that was all totally serendipitous when we could recognize who he was.
That he was a glass blower and get him to do it.
It was very delightful.
Tom McGlauchlin: Harvey and Clayton and I went home very excited Harvey was filled with possibility, realized that finally he was getting started.
And this was now where things were really going to take off.
And he was right.
Narrator: The success of the March workshop and a second held in June of 62 inspired Harvey Littleton to spread the gospel of glass when he wasn't persuading other universities to start their own glass programs.
Littleton was back at the University of Wisconsin teaching Future Studio Glass luminaries, including Marvin Lebowski, Fritz Dreisbach and Dale Kahului.
In turn, Littleton students graduated and started teaching Glass students of their own.
you think of the whole business as a family tree or Littleton as the roots and all these branches, well, a branch in very rapidly.
And you'd have third or third or fourth generation student teacher relationships.
And just three or four years.
Narrator: As the studio glass movement grew, Dominic Libino now returned to his Grand Rapids, Ohio, studio and picked up the Blowpipe.
Tom McGlauchlin: Nic Libino blew.
A lot more Glass and Harvey than those years.
From the second workshop in June, he'd gone home, built a furnace in his studio, and he blew glass every night.
He came home from work.
He had dinner, and he went out to the studio, and he blew glass until he had made eight pieces.
He wouldn't go to bed until he made eight pieces.
68.
I visited him and he had oh, I think there's four or 500 pieces of glass sitting on shelves and one room that he'd made in the previous six years.
Narrator: Dominic Libino knows prolific glass blowing quickly enhanced his skills, but it was his scientific acknowledge that helped produce some of the most beautiful glass ever made.
Jack Schmidt: I think the most outstanding characteristic of what Nick Libby did was the material He had such incredible knowledge of glass that he was able to make the material as good as it could be made.
And in fact, the glasses that he made broken and laying on the floor were far more beautiful than a lot of glasses sitting on the shelf.
Edith Franklin: Nick's glass literally sings when you look at it.
You'll look at his glass in a case and it's absolutely I just hear his singing.
Baker O' Brien: When someone shows me a piece of Labino glass to see if it's a real Labino glass, the first thing I look at is the glass itself before I even look at the form because the glass itself has a completely different look than than other studio glass The majority of people that run glass studios run a tank, a clear glass, and they buy their colors and bars from Germany, either Coogler colors or Zimmerman and they have they whack off a chunk of densely colored glass, hit that up separately and encase that in clear glass.
And that's where the color comes from.
Nick had science working for him when he first got started, and he had a whole world of scientific knowledge to draw on to mix his own colors.
So the glass is always mixed with the color inherent in the batch, which is why the glass has such a different look than most glass.
Tom McGlauchlin: His color was what really set his glass apart.
I mean, he had the most gorgeous colors because he was immediately melting from batch mixing the chemicals to make a particular glass that would utilize one particular color in cobalt, copper, silver, gold, whatever.
The whole form of the glass was designed to complement the color, and it always looked just perfect.
Harvey Littleton :Nick was not a trained artist, but he was an extremely sensitive person and creative person who could put together all of these things.
The Emergence series was where he really did his best pieces, and they were purely sculpture, and they were dependent on the color developing by the interaction of two layers of glass.
Two different glasses.
One over the other Those were, I think, quite an achievement Narrator: In the years following the 62 workshop, Littleton and Libino now became the recognized leaders of the studio glass movement.
And their groundbreaking work inspired studio glass artists worldwide The 62 workshops established both Littleton and Libby now as pioneers in the movement, but their paths would develop differently.
Harvey Littleton would devote many years to education before actively pursuing his own career as an artist.
Dominick Libino would concentrate on improving his skills and techniques before taking on a student to carry on his legacy of Glass A student sent to Libino know by his old friend, Otto Whitman.
Baker O'Brien: Well, I came here in 1975 as an Antioch student.
On a co-op.
I needed a co-op job for three months, and Otto Whitman had sent me out here to talk to Little Venus about architectural wrought iron and they took an interest in me because I wasn't a glass blower or a glass student.
And that's initially how I met them.
And I started out just being here for three months working on iron projects Well, I think that it was a kind of a relationship that really evolved over a period of time.
It wasn't like, Oh, you know, here this is the one I mean, there wasn't a week that went by that they weren't approached by someone wanting to come here and study people that already worked in glass, people from Japan, people from Japan that offered to come and like mow the lawn for an opportunity to work with him.
So when I showed up and I wasn't interested in glass, they were I didn't know it at the time.
I had no I had no idea that that was my end.
I just really wasn't interested in glass.
I only became interested in glass because I was here for so long.
It's hard to avoid around here Well, Nick decided that he was getting older and that I could be of use to him at the furnace if he trained me to work with the glass.
If you teach someone to work your way right from the beginning, then then they work the way that you work.
So he was taking, like, basic raw material and and training me to work and respect the tools and equipment in the way that he did.
He made all of his own tools and equipment for working in the glass or the annealing ovens he designed and made those himself.
He could weld.
He could.
He could do machining, fabricating the tools.
I mean, even some of the tools that I use today are Nick's tools that he has made He always quoted Edison when people asked him when he was going to retire.
He'd say a day or two before the funeral.
So and that pretty much sums up his life You know, it was hard to hold him down.
Narrator: Cancer was one of the few problems Nick Libino couldn't solve, but he could guarantee the continuation of his glass studio in the capable hands of Baker O'Brien.
Baker O'Brien: Even when he was very sick, he just expected that that I could do it and that I could do a fine job.
And there just wasn't anything holding.
There wasn't anything holding me back from from being able to do this, to be able to make the glass and to be able to carry on the studio.
So and that's what he really wanted to see the studio go on.
Narrator: Following his death in 1987, Baker O'Brien continued blowing Libino Glass with the blessing of Nick's widow.
Libby.
Five years later, Baker bought the studio and since then she has carried the Libino tradition into a new direction.
Combining Nick's formulas and color with her own unique designs.
Baker O'Brien: Blowing glass is a wonderful is a wonderful thing.
People get really charged about blowing glass and I'm right up there with them.
It's because it's so spontaneous.
It's so everything is so like now, now, now.
And that's why that's why I like I like music when I'm blowing, because it helps to sort of inspire and motivate me to move to a rhythm because there is so much rhythm going back and forth.
Every, every, every second counts It's like a dance because you're back and forth and timing is everything.
It's too hot, too cold, too hot.
You lose your form, too cold.
You lose a piece.
So when the glass comes out of the furnace and it's molten hot on the pipe, it's about 2100 degrees.
And then it probably ranges while you're working it between 16 and 2000 1900 maybe.
So then when it goes into the kneeling oven, it's usually cooled down to about 1200 degrees.
So it's everything is timing in terms of knowing how long it's in there, how long you needed to be in there for, what your next step is, and then and then bringing it out and getting it over to the bench as fast as possible to be able to do it in there, to do it.
That My pieces tend to be strong and simple and in bold and in deep colors.
I like rich color.
I like a lot of color.
I've always been really partial to functional work.
I I've always enjoyed using functional art and functional.
I mean, to me, there's nothing more beautiful than a simple bowl in a fabulous color.
The color is inherent in the glass, so the color goes all the way through.
It's not a veneer of color.
So right there, that's that's different.
The colors that I'm mixing in the furnace will have a different look from one angle, from one light to another.
They'll look green in one way.
They'll look blue in another way.
Reds in the silver glasses are the more difficult glasses to do with any sort of like predictability.
The oxidized glasses are easier that way.
Your greens, the blues, the purples.
I mean, those are those are beautiful colors.
And I like to I like to mix those colors.
I never mix like a straight green or a straight blue.
I like them to be different, to have a different look Well, the ball's a heavy ball, so it starts out in a form that's basically a bubble because you're introducing air into it.
And then it's the is attached when it's at the right consistency and when it's at the right, when the walls are the right thickness, because you're that's the time that you're introducing the air to it.
So you're actually finishing the bottom first and then attaching upon a rod and then opening the other end up.
So your shape is predetermined by the shape that it is before you put the penny on it.
The optic base that I do is placed in an optic mold which actually makes chill marks at every six points.
And I call it an optic based because I'm using an optical, but also because it gives it an uptick effect.
And then I use another tool to pinch around that part.
And so what it does is it really throws the light around almost in a cut way at the base, almost like if it was a cut glass I think each one has a life of its own.
A big reason that each one has a life of its own is because it is it is handmade I'm the only one that's making my work.
So each one has its own personality.
I can make six or something and each one is going to look a little bit different but I could make 20 of something and they're going to look a lot different.
And especially depending on the glass, if the glass is one that I'm using, that that's very changeable.
Then then they're going to look very different Well, I run at least one furnace all the time, so I'm always doing something with the hot glass.
I get more inspired with three because I get I have a pallet of glass to choose from.
I it, it gives me a broader range of what I can do when I've got three furnaces running.
Three furnaces is very expensive.
So I mean, it's that it's not a really cost effective way to make glass what I do, it's not cost effective at all, but it's the only way to get those kind of colors that, you know, that are the tradition that I've learned.
And it's the if I, if I was told that I couldn't do this anymore and that I can't make this kind of glass anymore, I don't I think I'd do something else.
Shawn Messenger: when I walked in to the glass department when I was in school, I, I mean, I just it was love at first sight.
I just walked in, my mouth, dropped open.
I just was blown away.
And I came home and I told my parents, this is what I'm going to do.
The rest of my life, I mean, that's I just knew it.
I just walked in and said, this is it.
Narrator: Recognized nationwide.
Sean Messenger creates lush floral landscapes and glass inspired by nature and the great impressionist painters.
Shawn Messenger: When I was in school, I thought I wanted to paint.
I went in to the studio and I hated it.
I hated oil painting.
I hated the smell of turpentine.
I couldn't wait to get out.
And I think I just sort of turned my glass into to paint before I had my own studio, I blew glass out of Crosby Gardens.
The doors would be open when it was hot.
So I would watch all the trees blossom and all of the the flowers bloom.
And I think I've always done this with my work.
I've kind of looked around my environment and picked up ideas from that I just slowly started thinking about Impressionist paintings and a lot of Monet paintings, and I guess that's where I took a lot of my inspiration from.
Narrator: Shawn Messenger shares her Toledo studio with her husband, Jack Schmidt, renowned for his one of a kind sculptures of metal cut glass and blown glass.
Jack Scmidt: It's difficult for two people working in glass to work together and be doing different things, but I really appreciate what she's making.
I mean, the form has to be right or the piece is just not strong.
And even if you make that form over and over again, there's still subtle differences.
And getting it just right makes the piece sing.
Shawn Messenger: Usually I have at least two assistants.
Heather is usually setting up the pieces, setting up the Marines Mike is actually lots of times finishing the pieces.
I'm sort of in the middle, back and forth, telling her what to do, telling Mike what to do.
And I'm picking up all of the color that actually makes the piece.
Narrator: Shawn's work is acclaimed for its rich color.
She uses powders, canes, rods and chips of glass, as well as dozens of colorful, handcrafted composites called Marines.
Shawn Messenger: Well, a Marine, she comes from the Italian techniques.
It's layers of glass.
Several different colors layer them over each other.
You put them on hot.
And it's sort of like dipping it in a candle, making it bigger and bigger.
It's the same process, only it sort of sort of reverse And at one point, you put in the hot bit into a mold, which shapes it in a shape of a star or several, you know, pointed stars.
Then we put crystal on all of them because if they were sat next to each other, they would they would become one.
So we don't want the crystal separates them to look like the flowers.
And then you heat it up and take another panty and attach it to the end of the hot bit and then pull it into long.
Canes and then let it cool.
When we when we pull the Marines, we also try to make them different sizes because flowers in nature would be different sizes.
We have specific flowers in mind when we're making them or different names for them.
Red roses.
Pink roses, Morning glories.
Daffodils.
It's so amazing what what nature creates.
You know, if I could come back and make just a little bit of that, then I've accomplished something.
I think once it's cool, then all the pieces they're cut up into two small individual pieces.
Using a pair of nippers.
And you just sit there and click, click, click away at all.
Of them to make him into all the individual Marines.
After they're all cut, then they're all separated into their own little compartments.
And from there, you get to create, you know, whatever you're doing, all the landscapes you get to create, the gardens you pick and choose, the small pieces, the large pieces, and you put them together into fields of color I made a perfume bottle.
It's a teardrop shape.
It's got a little like bouquets of flowers around it.
Daisy.
The yellow daisy.
And the other one is actually the hippie daisy, we call it.
It's yellow and orange.
People collect perfume bottles, collect them, and have, you know, vast collections of perfumes other people collect them and just put them on their dressers.
You know, do it as a decorative piece.
First, we start with the background color.
We gather the glass and add whatever color background we're going to do.
To it.
We roll it in the colors, and then it's heated in to the surface.
Another layer of crystal goes over that and one of my assistants will usually bring me a bit of hot color.
It's usually two colors and overlay color that's added on to the glass that's fuzed in.
And then we have small canes that are like the little stems.
We just pick those up from actually the Marva, and then we add the Marini side And all of those are fuzed into the surface.
There's another layer of crystal that goes on after that.
And then from there is when I start flowing and shaping the piece you use a lot of tools a lot of times, but I personally like the newspaper, the wet newspaper, because it's in your hand.
It's, you know, it's just it's just between you and the glass.
That's the only thing that's stopping you from touching the glass.
But it's you're using your hand to create the shape.
I like it far better.
Than using any other tools.
Jack Schmidt: One of the things that influences me to a great extent from Shawn is her constant enthusiasm about working with the material.
And she's been a workhorse dealing with this material ever since she first saw it.
And every day she comes into the studio, she just dives back into it.
She loves the material.
She loves what it does.
And it's that to me is very stimulating to see somebody that can re-approach that material every day with that same kind of interest and enthusiasm.
Shawn Messenger: There's just sort of a magical thing that goes on when you're blowing glass.
I can't imagine doing anything else.
There's so many things about it that are so incredible.
And every day I kind of discover something new.
It's just a lot of fun and a lot of excitement.
That goes on in my life.
So I can't imagine doing anything else.
Narrator: Artist Mark Matthews works in the Hot Glass studio at Sauder Village in Archbold Using a simple shape so familiar from childhood to create fantastic worlds of color and pattern.
Mark Matthews: Previous glass order at the village made marbles, and I made him show me how to make one.
And I immediately had this idea for these huge containers, radically different spheres, And the quest for different color combinations and different formats and different graphics has just been pretty well an ending for 15 years.
Oftentimes I have elderly people who look at these figures and they say, I had things just like this when I was a kid.
Well, I know for a fact what the antiques look like.
And mine are so idealized and so meticulously produced compared to that.
But what's happened with these people is they have had genuine, esthetic experiences with these things in their youth.
And it's been 60, 70 years since they've handled these things.
And these things have become mythology in their mind.
The 19th century objects were just disposable.
They were just toys.
They were never meant to be priceless artifacts.
They were produced in mass and the not enough care was taken to make them dazzling enough to be salable.
But they were never meant to be archival objects.
Narrator: Mark Mathews spheres are worlds apart from the marbles we played with his children.
His glass art is in the permanent collections of some of the world's greatest galleries, including the Smithsonian Institution and the Victoria and Albert Museum in London.
Mark Matthews: The sphere itself is just a it's just an excuse for an object.
It's an excuse for a glass object.
It's a it's a minimal physical unit that can hold just about any idea.
It's kind of a neutral physical unit.
Anywhere from the softest floral sort of color schemes to to the hardest black and white geometric to to an empty space with a articulated air bubbles.
The sphere is really just a neutral unit that's accepting of any sort of an idea.
Narrator: Some of Mark's most admired and intricate designs are his animal print spheres.
These incredible creations are accurate reproductions of animal pelts held in the archives of the Smithsonian Institute.
Mark Matthews: They're just they're just really lush.
They're really lush exercises in fantastic patterns.
They're patterns.
I couldn't possibly come up with the drive with them was always to make the patterns just absolutely as accurate and specific to an individual beast as possible to avoid any kind of a cartoon or a superficiality or a superficial design or anything.
The world is awash in cheesy animal patterns.
This is this is this is reality.
This is this is stem to stern incorporation of the thinking all the way arou I had the idea for a marble with a reversing twist, onion skin kind of a pattern.
Onion skin is a is a term used for antique marbles that have tiny flecks of colored glass between the layers of the clear, often with a white background to reflect the transparent color.
But this this onion skin pattern that we made is a reversing twist.
So there's a Chevron at the equator and it twists in opposing directions and posing helical directions to two.
Each pole had five different transparent colors that ranged from sort of an orange this red through like a bluish purple with everything in between and then we had three different chartreuse based colors.
And these were opal glasses that were applied over the transparent and the transparent were applied over the the enamel white and then the last step was to put on the adventuring green, sort of a green glittery glass.
It's very emerald in color.
With flecks of mica, make the make the reflections we start with an accumulation of of clear a sufficient amount to be underneath the enamel, the white enamel glass, which is put on in the form of a powder layer, clear is put over that.
And the heat from that layer, clear is used to pick up the first layer of red, which is all the transparent pinks and and pinks and lavenders.
And that one orange and then it's heated and that's melted in and one at a time each of the greens is put on there's a control of exactly which colors are chosen and exactly the size of the chunks of color used.
But other than that, there is a sort of a randomization.
What ends up at the equator on a particular sphere is there's a happenstance aspect to that.
And everything that the glass has got to be done completely relevantly to the glass the glass is really telling me what to do.
I have to respond to it.
I can only do with it what it will have done to it.
I'm really interested in glass history.
Glass history is huge.
It goes back almost 5000 years and to a studio glass artist oriented like I am.
It seems like this whole huge history of glass is sort of a playground.
So you can pick and choose and recombine and and learn to think in all these different major, major techniques.
Narrator: Mark's fascination with history takes physical form in a special piece created from a remnant of the glass industry's illustrious past.
Mark Matthews: The the the actual mold for this is actually an original and original living mold.
It's an iron mold that makes a small diamond impression about the size of the tip of your index finger.
And then it can be cast over and everywhere.
This little dimple, it catch a little air bubble.
They were used for for decorative applications on pieces, for stems and goblets, for feet, feet on vases, a big vase with perhaps three double ball feet.
And the story is that they were scrapping the old factory a the old the old hand plant that Libby shortly after World War Two.
And they were taking everything to the to the junkyard everything all the pipes and all the old hand molds and all the optic molds and everything.
And Sid Hag Doll, who was the head of the furnace department he managed to scrape together two or three pallets of these antique molds and stashed them under furnaces that were under his jurisdiction.
And that's how any of them still exist.
We're going to make a series of spheres that are probably about an inch and five eighths in diameter and in a gold ruby pink glass.
To make this pink bubble sphere, I'll take a very small gather, perhaps the size of your little finger, very white hot, and drool it down into this mold.
The biggest trick is entering the mold because the mold has such a small orifice to get the glass down through to that little indentation pattern, then it has a sort of a stem to it.
Before it gets to the idea of it where where the actual diamond pattern is.
And that that stem going down there will have some chill marks on it.
And so in order not to have a froth of unsightly bubbles that don't relate to the bubbles in perfect rows, I will fire polished that little shaft and then let that cool off and then I get a second layer of the pink glass over that, and that's when I'll catch the air everywhere.
There's little dimple, I'll catch a little bubble, then I'll form the sphere so these are these are just these are done one at a time, one after another, each one on a separate rod well, as the sphere is cracked off, it's got a little stem where it was last attached to the to the stock or to your your panty rod and this can be softened with the torch.
And there's a little bit of crud there from the tooling that needs to be gathered up over the sheers and pulled off also that mass has got to be removed so that what's left can be incorporated in the sphere with the with the finishing tool Narrator: mark.
Matthew's work incorporates one part history and one part sculpture in a molten recipe that produces breathtaking treasures destined to be admired for generations.
Mark Matthews: And I like the idea of extremely durable objects.
There's something about it.
The objects can enclose extremely delicate things or have just hair fine patterns in them that look like lace.
But the object itself is is like a rock roll down a hill and still be in one piece, whereas a dragon's stem gave it think or excuse me, there fell over in it.
Narrator: The studio glass movement has spread rapidly in infinite directions since that first workshop in Toledo.
In March of 1962.
The choice of what to make has been placed firmly in the hands of the artist, passed down from industry and passed on to us.
Harvey Littleton: You can't compare glass blowers from industry to us.
The skill to blow glass as an artist is the skill to make each experience a richer one.
To make each form better, or as the skill of a man in a factory is to make each piece the same as the one before, because that's what the factory is selling now.
They've got a bubble in the stem.
They've got a bubble the same size in every step.
Or as we don't do that, we make everything different that's what it is to be an artist.
of course, the glass movement has just grown incredibly it's.
It's unbelievable how many people are making glass now.
The quality and quantity of work being done today is just light years ahead of where it was in the sixties, and it's gone very intensely in all directions.
It probably boggles Harveys mind sometimes to see how far and wide it's gone, you know?
But I think he fully anticipated it, you know, I think he was a real visionary that way.
Harvey Littleton: It's sort of like Alice stepping through the looking glass, who would believe what was behind their look.
You know, who would know people ask me, Did I know?
No, I didn't know.
Did I dream about it?
Sure.
Every damn night I dreamed about making glass what could be made.
Support for PBS provided by:
Toledo Stories is a local public television program presented by WGTE